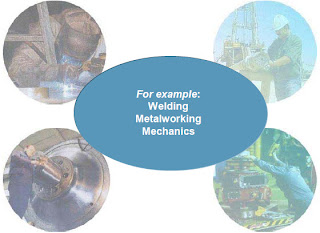
A work center is an organizational unit within an operational system.
A work center can be one of the following:
- Machine
- Group of machines
- Person
- Group of people
In SAP Plant Maintenance, work centers are used as:
- Main work center in the master record for the equipment or functional location
- Main work center in a maintenance item
- Main work center in the task list header
- Performing work center in the operations for a task list
- Main work center in the order header
- Performing work center in the operations for an order
Work centers belong to the master data in PM and provide the capacity required to perform a task.
Contents of Work center:
The basic data contains general data such as work center category, description, responsibility, and usage.
Work center links provide the connection between work centers and other objects within the SAP System. You can link a work center to the following objects:
- Cost center
- Qualifications
- Staffing positions
- People
Main function of Work center
- Costing: You can use costing to determine the costs of an internal activity by a product unit. The aim of costing is to attribute the costs incurred to the individual cost objects. It uses the work center to link the operation to cost accounting by maintaining cost centers and activity types. If the work center is used in an operation, standard values can be entered for the activity types specified in the work center.
- Scheduling: You can use scheduling to determine the dates when operations should be performed. For this, the time required for the operations must be calculated and compared with the time available in the work center. The standard values and quantities in the operations are used as the basis for this calculation. During scheduling, the start and end dates for the operations are calculated from this data using formulas, which have been entered for scheduling in the work centers.
- Capacity planning: In capacity planning, the capacity requirements for the operations in the orders are determined and compared with the available capacity defined in the work center. During capacity planning, you can use work center hierarchies to aggregate (at higher-level work centers) the available capacity and capacity requirements of lower-level work centers.
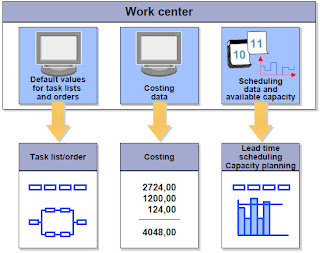
Example of Work center capacity screen:
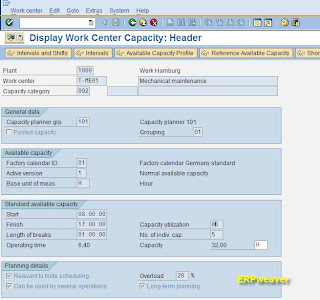
No comments:
Post a Comment